Why OEMs Use Innovation and Technology as a Barrier
Why OEMs Use Innovation and Technology as a Barrier
—and how the Aftermarket Responds
When desktop printing first took off, there were only a handful of printer models, and many OEMs used the same devices but simply put their own badges and brands on them. Nowadays, there are only a handful of printer brands, by comparison, but OEMs launch new printers and new consumables quite frequently.
It is useful to ask if these new products are embedded with new innovations which might benefit end users and/or the environment. Do end users really want all these new printers or is there a reason behind all these new printers hitting the market?
Cartridges, chips and firmware upgrades
Originally, the OEMs did not put chips on their inkjet and laser toner cartridges. Then, in the 1990s some OEMs started to add a simple memory chip to their cartridges. The functions of these chips were to store cartridge information, such as ink or toner levels and manufacture dates and to communicate with the printer.
Then, third-party manufacturers started to offer cost-effective remanufactured or new build compatible cartridges to end users and captured market share from the OEMs. In response, the OEMs started to develop sophisticated micro-controller chips with encryption technology and placed them on their cartridges. Was having these costly, encrypted chips for the benefit of end users?
Of concern to end users, however, is not knowing what personal information was being captured and stored in these “black box” chips. Should the end-user destroy these chips before they dispose of the used cartridge?
By using encrypted chip technologies, the OEMs managed to delay the entry of aftermarket chips and third-party cartridges from reaching the market by at least one if not two years. The OEMs have enjoyed this monopoly period to sell their expensive cartridges.
Once aftermarket chips were researched and developed and made available, the OEMs started to upgrade their printer firmware frequently. This caused cartridges using aftermarket chips to not work properly in OEM printers.
To what extent will the printer OEMs go, to continue with technologies like this? Recent rumors suggest that OEMs will use cloud-connected chips to authenticate a cartridge when it’s installed in a printer. Again, do end users really need a higher cost, cloud technology chipped cartridge? Who is getting the benefit here?
The twisted triangle, dongle driving gear
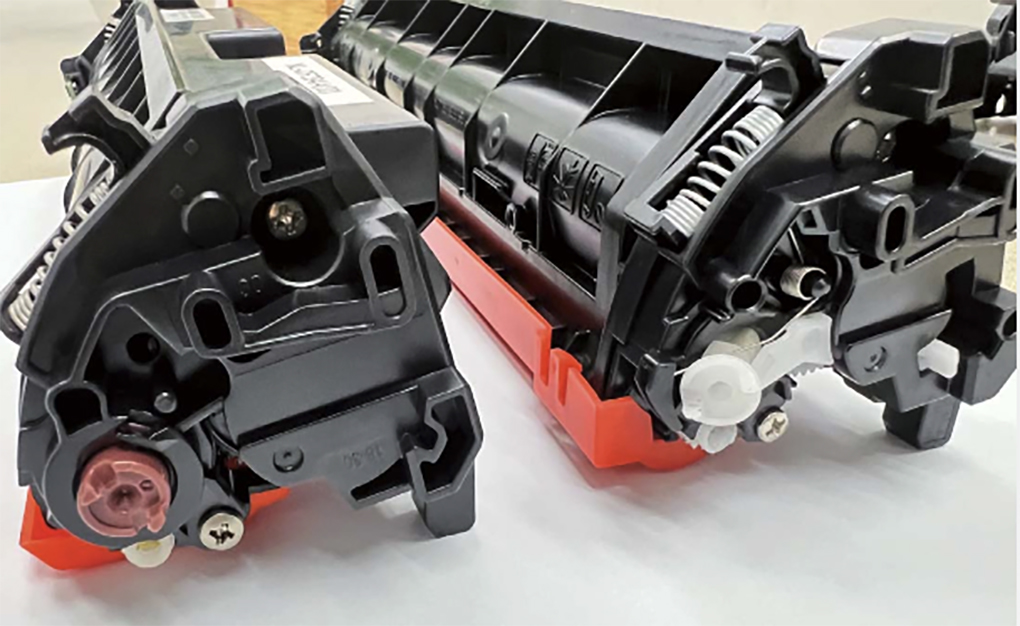
Print-Rite’s reddish-brown zero-twist gear (left) is a complete redesign of the OEM patented dongle gear (white, right).
Originally, the OEMs used a simple coupling mechanism to drive the toner cartridge in the printer. Then, the OEMs started to use a twisted triangle coupling mechanism to drive the toner cartridge in the printer.
The aftermarket took on the challenge and researched and developed a design around solution: the “No-twisted gear.” Even before the twisted triangle gear patent had expired, the OEMs developed and started to use an even more complicated coupling mechanism, known as the dongle gear.
The ongoing development and advancement of these technologies increases the cost of a cartridge and it’s the end user that needs to pay for it. Why do the OEMs put a lot of effort into engineering and focus on intellectual property lawsuits on the driving mechanism of a toner cartridge? Why was there a need to alter the driving mechanism from something simple that worked, to a more complicated mechanism?
A laser printer can only work with an effective coupling mechanism with the printer cartridge. So, the invention and patenting of the dongle gear allowed the OEMs to pursue lawsuits with those who infringed while delaying the development of non-infringing third-party consumables.
Most of the aftermarket copied the OEM design. Very few, like Print-Rite put in engineering efforts to develop a “no inclination dongle gear” which would not infringe OEM patents while working properly in the printer. It did delay product time-to-market and increased costs.
End users just want a good quality, easy-to-use, low-cost toner cartridge. It is not difficult to establish who was the only beneficiary of the twisted and dongle gear technologies.
Chemical toner powder
Conventional toners, which use electricity to pulverize the material into small particles mechanically, were the first to be used. With new advancements, some OEMs use chemical toner powder in the toner cartridge instead. Chemical toner production methods are either suspension polymerization or emulsion aggregation.
Chemical toner production uses a significant amount of water in the production process. Additional energy is required to recover, treat, and release the water back into the environment.
The truth is some OEMs invested heavily in the development and production of chemical toners. It is not an energy-saving strategy and the huge amount of water used to produce chemical toners is an environmental concern.
Has the development of chemical toner become a technology barrier for the aftermarket? Recent aftermarket advances in lower melting point resins and pulverization and sphereolizing techniques allow for the more efficient manufacturing of conventional toner to generate smaller and more consistent particle sizes within a narrow particle size distribution. These improved aftermarket mechanical toners can be a cost-effective alternative to chemical toners.
Regional inkjet and toner cartridges
Another OEM strategy is to develop a unique cartridge to only work in select regional markets. They contain a regional chip and a regional mechanical structure.
These regional printers and cartridges increase the manufacturing, logistics, and SKU management costs. The OEMs do it because it makes remanufacturing more difficult however, it causes more waste to end up in landfill.
Both the aftermarket and end users recognize the disadvantages and prefer to use a universal cartridge. The aftermarket developed universal, compatible cartridges by changing the cartridge structure and adding a universal chip. Distributors also enjoy having less SKU management.
Over-engineered cartridges
The OEMs have over-engineered the printer cartridge which do have additional features and components that improve performance. However, being more complex has increased the costs.
Listening to end-users
We all know that those involved in product development and technology advancement need to listen to the end users’ voice. Do end users need a cartridge with a sophisticated chip and a complicated dongle gear drive? Do they need chemical toner? Are they wanting an inkjet cartridge to print less than 100 pages and a toner cartridge to only print 1000 pages?
The “razor-and-blades” business model used by the OEMs means they must try to stop the use of third-party compatible cartridges. They will use technology and intellectual property rights barriers. What they really want is to sell more “low page yield” cartridges at higher costs.
There are some excellent aftermarket manufacturers. They respect OEM inventions. They have also inventions of their own that benefit end users and the environment.
Print-Rite, for example, is a pioneer of refillable toner and inkjet cartridges. These allow end users to refill their toner and ink which helps them to save money and help the environment.
Some Print-Rite inventions include:
- “Continuous ink supply system” (CISS) which allows users to print more than a thousand pages instead of hundred pages with an OEMs ink cartridge.
- The “Smartact” cartridge (featured on the front cover of RT ImagingWorld magazine) has the waster hopper removed and it continuously reuses any surplus toner without it ending up being thrown away.
- “No waste toner” toner cartridge which reuses the waste toner allowing the user to use all the toner in a toner cartridge and providing a six-fold page yield.
- The “Foamless ink tank” design can increase ink content with the same cartridge footprint. It reduces residue unused ink.
The aftermarket puts a lot of effort into reducing costs. They redesign the toner cartridge to be made on automated production lines to lower production costs while providing consistent high-quality cartridges. There is no need to copycat the OEM designs.
Innovation, technology advancement and intellectual property should bring better products to the end user and the environment. They should not be weaponised for the sake of competition.
The aftermarket respects the OEMs’ inventions and intellectual property rights and will continue to offer better non-infringing workaround solutions for end users. The OEMs can consider competition and innovation from the aftermarket sector as motivation to improve.
This article, “Why OEMs Use Innovation and Technology as a Barrier” by Philip So was the front cover story of the RT ImagingWorld magazine which can be downloaded for free.
At the time of writing, Philip So has been with Print-Rite for 22 years and is Chief Engineer. He holds a Master’s degree from the University of Hong Kong, is a Member of the Hong Kong Institute of Engineers (MHKIE) and is a High-level (Level 1) Innovative Talent recognised by the Zhuhai government in China.
You can contact Philip So at philipso@print-rite.com.cn
Related:
Comment:
Please add your comments below about this article, “Why OEMs Use Innovation and Technology as a Barrier.”
Leave a Comment
Want to join the discussion?Feel free to contribute!