Automation: to be or not to be?
Automation: to be or not to be?
Innogetic’s Henry Cheng urges industry to move to ‘big data’ automation without delay
Just because a manufacturer boasts it has an automated production line, does not mean that company is receiving and passing on the full benefits it may have expected from the investment.
When I first moved to Zhuhai in 2010 to live and work in the heartland of the global imaging supplies industry, the enterprising owners of the companies prided themselves in the size of their workforce. After all, China had become the world’s factory and it was on display with the tens of thousands that were working in Zhuhai factories on OEM, remanufactured, and then fully-manufactured compatible printer cartridges. At the time, wages were low, and it was a matter of pride to show off the size of the factory in terms of space as well as the number of employees.
However, China has changed. In less than 20 years, 400 million people have been pulled from poverty, and another 400 million now make up a middle- class owning apartments and motor vehicles—a much larger number than the total population of the United States. It’s a remarkable achievement. However, wages have increased, and it is not as cheap as it was to manufacture goods in China.
Today, the same factories are quiet about the number of employees they have and prefer to share how they have embraced modern industrialization and adopted automated production lines.
Henry Cheng (pictured above) is the founding President of InnoGetic Technology Co Ltd (Innogetic), an enterprise founded in 2011 to deliver effective and efficient automation solutions to a wide variety of industries, including imaging supplies.
“Automation is not new in the manufacturing world. It’s been widely used and has been established in the United States, Germany and Japan since the 1980s,” he said. “In some ways, China is only just catching up. Because it has to.” Cheng explained that as labor costs have increased, manufacturing costs have become uncompetitive and unsustainable. “There are only two ways to solve this,” he said.
“You move your production to a low-wage, low-cost region. Or you move to automation. Automation is the only chance for survival.”
The first industrial revolution was marked by a transition from hand production methods to machines through the use of steam and waterpower between 1760 and 1840 making an impact on textile manufacturing.
The second industrial revolution, known as the technological revolution, occurred in the period between 1871
and 1914, and was due to advances in transportation and communication. “Industry 2.0 saw the world adopt
mass production thanks to improved methodology,” said Cheng. “This helped increase output levels.”
Industry 3.0, which was the digital revolution, occurred in the late 20th century. The advent of computers assisted the production process and machinery began to abrogate the need for human power. This is where automation came to the fore.
Quick Move to Automation
Chinese companies jumped onto the automation bandwagon later than western countries. The Chinese government has now set targets and is providing financial incentives to drive change. Cheng is convinced, however, the need to lower the cost of labor is the real motivation for change.
“Of course, there are many more benefits,” Cheng added. “Automation can deliver consistency in the quality of the manufactured product. The dependency upon human labor and human error is removed. High-end production together with high-quality results are additional drivers for automation.”
I asked Cheng in what ways has Industry 4.0 made such a seismic change to manufacturing and production. “Industry 4.0 is about the smart factory,” Cheng said. “You could also call it ‘intelligent manufacturing’ and different countries have different names for it. 4.0 has only been possible because of the legacy it inherited from 3.0 and 2.0.”
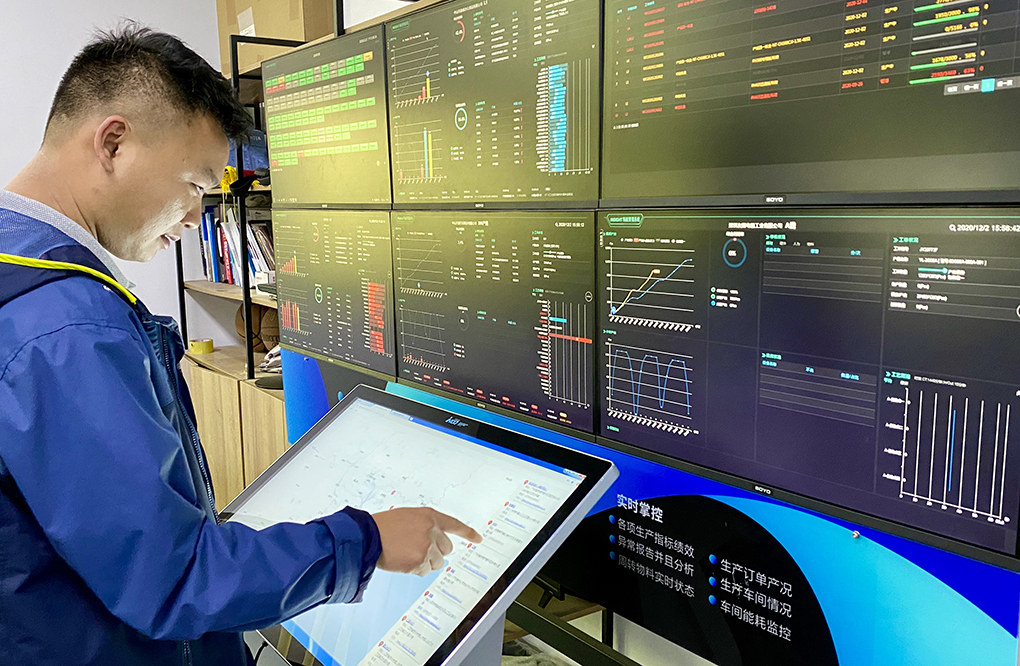
According to Cheng, Industry 4.0, Automation 2.0 or Intelligent Manufacturing has made a huge impact on the industry chain. It has everything to do with the data that is captured during production that can be fed back to management. This relates to machine optimization, the meeting of targets, raw materials, as well as finished goods.
According to Cheng, Industry 4.0, Automation 2.0 or Intelligent Manufacturing has made a huge impact on the industry chain. It has everything to do with the data that is captured during production that can be fed back to management. This relates to machine optimization, the meeting of targets, raw materials, as well as finished goods.
Under an Industry 3.0 model, a factory had to order all its resources and store them ready for use. With access and the speedy analysis of data, management is now able to reduce the stock being held and also reduce the amount of warehousing needed. “You can have your data linked with the suppliers of the raw resources in your industry chain to provide ‘just-in-time delivery’ to match your production needs,” Cheng explained. “At the same time, your downstream buyers and customers can also be putting their needs into your system and this will drive the production lines to make the products you mostly need, when you really need it.” This also reduces the need for warehousing.
Cheng claims the real value of automation is best implemented when the whole supply chain processes are considered rather than just the individual process.
Warning
For whatever reason, many senior managers have rushed to install automated production lines without really considering what they really need. “You can easily spend US$100,000 on a single step in the production process,” Cheng explained. “Yet, there is the real possibility you may never get a return on investment (ROI).” Cheng has seen factories spend a king’s ransom to move into automation without really understanding what they are doing, only to see the production line or parts of a line scrapped a short time later because the production process changed.
A lot of downtime is needed when an automated line needs to have maintenance. “I have often seen a whole line shut down for days because just one part of the line broke down and was waiting for new parts to be installed,” Cheng said. “The whole line, worth millions of dollars, was shut down.”
Production lines also have to be shut down and reset when you simply want to make a different version of the same product. “Let’s say the toner in the cartridge usually contains 200 grams, but then you want to do a ‘run’ with 300 grams in the cartridge,” Cheng said. “The downtime could be many hours while the changes are put into place.”
In his view, Cheng believes the best way forward for industrial evolution, especially in China, is to jump to Industry 4.0 with the introduction of “Big Data” informatization in the production process. At that stage, he and his team at InnoGetic look at transitioning a manufacturer from the Industry 3.0 model to ensure the ROI benefits are achieved having given consideration to technology maturity and the product life cycle.
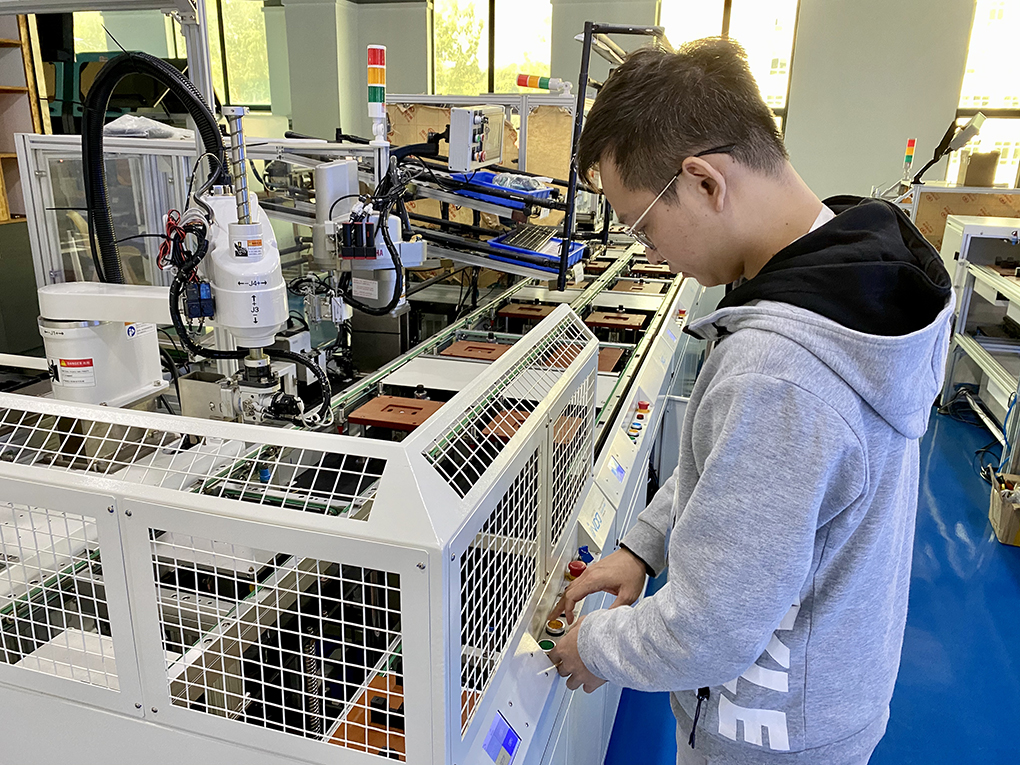
“In some circumstances, integrating people with machines may provide higher efficiencies, more stable and higher production levels and a solid ROI than a fully-automated line,” Cheng said.
“In some circumstances, integrating people with machines may provide higher efficiencies, more stable and higher production levels and a solid ROI than a fully-automated line,” Cheng said.
“The smarter solution for automation may be to have the flexibility where humans work with the machines. The middle-level engineers are still analyzing the data, resources still arrive just-in-time, but when a particular part of the line needs service, or where it is simply more cost-effective to have humans completing a specific task, the manufacturing process is not held up,” he said.
Cheng said this model also provides a shortcut for manufacturers wanting to enter the game with less investment in time and money.
Apart from Cheng himself, InnoGetic has staff with world-class experience with the top 500 global enterprises in Europe and the U.S., industrial and engineering experience with supply chains and management, and the know-how to maximize production output to gain true competitiveness.
“InnoGetic can really help here,” Cheng said. “We work simultaneously with management and challenge them to consider what they really need, design a system where humans and machines work side-by-side, and then work with them to monitor and analyze the data, tweak the processes and then deliver good quality results, profitably.” ■
Contact Mark Chen for more information via email at Mark.chen@innogetic.com or by phone at +86-150-1746-7526
Related:
- Automation Accelerates Transformation
- Ricoh to Automate Production Process
- Additional Automated Line Delivers Higher Quality for Ninestar
- Print-Rite to Ensure Quality with Automated Copier Toner filling production line
- RSA Launches New Software for Print Automation
- Automated Offices Provide More Time – Berto makes coffee
- High-end Automation Manufacturing Park Breaks Ground
Comment:
Please add your comments below about this feature article, “Automation: to be or not to be?”
how to contact them?
Hi Vincent. You can contact Mark Chen for more information via email at Mark.chen@innogetic.com or by phone at +86-150-1746-7526